Die Bauckhof-Hafermühle für Bioprodukte
Bauckhof - Weltmeister in glutenfrei
Die Bauckhof-Hafermühle für Bioprodukte
Bauckhof - Weltmeister in glutenfrei

Die Bauckhof-Hafermühle für Bioprodukte
Bauckhof - Weltmeister in glutenfrei
Im Norden Deutschlands, in der Lüneburger Heide, steht eine der modernsten Hafermühlen Europas. Schon von Weitem sehen Besucher das große silberne Gebäude. Aus ihm kommen ausschließlich Bioprodukte – glutenfrei in höchster Reinheit. Die Mühle der Bauck GmbH ist effizient und eine Investition in die Heimatregion.

Geschäftsführer Jan-Peter Bauck trifft Anfang 2017 die Entscheidung zum Bau der Schäl- und Feinmühle für glutenfreie Biolebensmittel – immerhin eine Investition von rd. 24 Mio. Euro, die 40 neue Arbeitsplätze schafft. Nach langer und sorgfältiger Planung entsteht 2020 in Rosche ein achtgeschossiger, 45 m hoher und 25 m breiter Gebäudekomplex mit einer Verarbeitungskapazität von mehr als 20000 t Getreide im Jahr.
Der Bau der neuen Mühle ist ein Gemeinschaftsprojekt der Firmen Schule und Kastenmüller. Die Schälmühle wird von der F. H. Schule Mühlenbau aus Reinbek gebaut, die Feinmühle zur Vermahlung von Hafer und anderen glutenfreien Produkten von der Firma Stefan Kastenmüller aus Martinsried.
Schulz Systemtechnik aus Visbek setzt das Automatisierungskonzept um und die Verpackungsstraßen stammen von der Rovema GmbH aus Fernwald und PremierTech. Das Gebäude und die Außenanlagen werden von der Fa. Agravis als Generalübernehmer erstellt. Gefördert wird der Neubau vom Europäischen Fonds für regionale Entwicklung und der Gemeinschaftsaufgabe „Verbesserung der regionalen Wirtschaftsstruktur“.Der Baumeister der Mühle ist Jan Gausepohl. Er ist Müller in der dritten Generation und lernt sein Handwerk an der Deutschen Müllerschule Braunschweig (DMSB). Danach arbeitet er für zwei große Mühlenkonzerne. Sammelt Erfahrungen bei Mühlen weltweit, u. a. in Kasachstan und Nigeria. Er macht sich selbstständig und kommt 2016 nach Rosche zur Bauck GmbH. Deren Feinmühle hat ein technisches Problem. Gausepohl löst es und versteht sich so gut mit Jan-Peter Bauck, dass dieser ihn bittet zu bleiben. Denn er braucht für seine Vision einer Biohafermühle den richtigen Mann.


Jan-Peter Bauck hat die Bauck KG von Onkel und Tante übernommen und die Bauck GmbH gegründet. Für seine Mitarbeiter ist er nur „Jan-Peter“. Mit der Biohafermühle will er 180000 Transportkilometer pro Jahr einsparen. Zusätzlich fällt der ganze Aufwand für die Begleitung der Waren und die Qualitätskontrolle weg, wenn alle Produktions- und Prozessschritte in einer Hand sind. Jan Gausepohl gibt für die Hafermühle seine Selbstständigkeit auf und zieht in den Norden.
Weltreise mit Hafer
Im folgenden Jahr reisen die beiden Männer mit ihrem Projektleiter Dieter Projahn einmal um die Welt und besichtigen Mühlen. 20 ppm sind die gesetzlich zulässige Höchstgrenze für glutenfreie Lebensmittel. Mühlen können weniger schaffen. Die letzte Etappe der Reise führt die Männer nach Australien. Auch dort ist in modernen Mühlen bei 10 ppm Schluss. Auf dem langen Rückflug diskutieren sie die Lage und Jan-Peter entscheidet: Bauck wird 5 ppm schaffen, was die derzeitige Nachweis- grenze ist. Sind die Qualitäten mal nicht so gut oder senkt der Gesetzgeber die Zielvorgaben, ist man dennoch auf der sicheren Seite.
Zu Hause in Rosche lässt Jan Gausepohl ein 3-D-Modell der computergesteuerten, vollautomatisch arbeitenden Anlage von der Firma Schule Mühlenbau entwickeln. Eine Komplettlösung für die riesige Mühle vorzudenken, mit ihrer Vielzahl an Prozessschritten von der Annahme bis zur Flocken- bzw. Mehlherstellung, dem Absacken und Verladen, mit all ihren Abläufen, Maschinen und Lagern, ist eine enorme Tüftelei. Zudem gewährleisten nur die optimale Laborkontrolle und Verarbeitung des Getreides die geforderte glutenfreie Qualität.
F. H. Schule Mühlenbau
2019 geht es los. Nach intensiven Beratungen mit verschiedenen Anbietern bekommt der nur 90 km von Rosche angesiedelte Maschinenbauer Schule Mühlenbau den Zuschlag für die Anlage. Für diesen weltweit agierenden Schälmühlenhersteller spricht seine Spezialisierung auf Maschinen und Sonderlösungen zur Bearbeitung von Getreide und Hülsenfrüchten; in Großbritannien baut er zurzeit die größte Hafermühle Europas. Dank der Spezialisierung auch im Bereich Maschinenentwicklung kann die Firma alle Komponenten mit Einzelnachweisen zur Lebensmittelkonformität der produktberührenden Teile liefern, was eine besonders herausfordernde Aufgabe war.

Alexander Bachur wird ebenfalls ein wichtiger Mann auf der Baustelle. Er ist Leiter der technischen Angebotsprojektierung bei Schule Mühlenbau. Für Jan Gausepohl ist die Hafermühle ein Lebenswerk. Hier fließt seine gesamte Erfahrung ein. Unter anderem aus energetischen Gründen entschließt er sich, die Mühle in die Höhe zu bauen. Die Hafermühle hat nur zwei Elevatoren, ansonsten arbeitet sie mit Druckpneumatik. Das ist hygienischer und spart vor allem auf den letzten Metern viel Energie. Nach einer ausgiebigen Reinigung mit Aspirateur, Steinausleser, Trieur und Farbausleser kommen die geschälten Kerne entweder direkt oder über den Trommelgrützeschneider zum Dämpfen. Danach gelangt das Produkt über den Flockenstuhl und Fließbetttrockner in den Fertigwarensilo.
Der Polizist
Wichtig ist der zweite Farbausleser. Die Mühlenarbeiter nennen die Maschine der Firma Cimbria „den Polizisten“. Er findet selbst noch Körner mit winzigsten Farb- fehlern. Alle ausgesonderten Strohteile, Sämereien, Spelzen, Körner mit Farbfehlern und Fremdgetreidekörner werden auf der ersten Etage der Mühle zu Tierfutter pelletiert. Ein wesentlicher Anteil des Ausschusses entfällt auf Haferschalen, die u. a. für die Futtermittelindustrie interessant sind. Die Pelletierlinie verarbeitet die Haferschalen mit den anderen stärkehaltigen Nebenprodukten, die mit der Flachmatrizenpresse zu Pellets geformt werden. Durch die Kreisbahn der Kollerrollen auf der Matrize entsteht Friktion; somit werden vor allem die nachwachsenden Rohstoffe zerfasert, bevor das Produkt in die Presskanäle gedrückt wird. Eine vorgeschaltete Vermahlung ist überflüssig und spart Energie. Durch die Komprimierung entsteht ein staubarmes, dosierfähiges Erzeugnis mit deutlich höherem Schüttgewicht, das Lager- und Transportkosten spart.

Sortierer und Lüfter
Auf der dritten Ebene der Mühle befindet sich die Schaltzentrale. Ein Mitarbeiter kontrolliert im verglasten Raum vor großen Bildschirmen den Produktionsprozess. Draußen findet ein harter Wettkampf statt: Die Schäler von Bühler und Schule Mühlenbau kämpfen darum, wer besser schält. Noch ist nicht entschieden, wer das Rennen macht. Auf dem Mühlendach steht die riesige Lüftungsanlage der Firma hdt.technik. 145000 m³ Luft verbraucht die Mühle pro Stunde. Ein Kreuzwärmetauscher verwandelt mit geringer Energiezufuhr verbrauchte Luft in warme Frischluft. Nur 24 kWh Energie sind dafür erforderlich. Dank u. a. der Fotovoltaikanlagen auf den Dächern der angrenzenden Gebäude, der Wärmeversorgung durch die eigene Solarthermieanlage für Warmwasser und der Fernwärme aus der benachbarten Biogasanlage arbeitet die Bauck GmbH klimaneutral. Energieeinsparung ist insgesamt ein wichtiges Thema. So wird zum Beispiel die Abwärme der Kompressoren für die Vorwärmung des Dampfes genutzt.

Seit September 2020 läuft die Biohafermühle. Sie verarbeitet neben Hafer auch Hirse, Braunhirse, Kichererbsen, Reis, Buchweizen, Quinoa sowie Mais und schafft 60 t Flocken und 48 t Mehl pro Tag. Die Mühle besteht aus drei Doppelwalzenstühlen mit Vario-Antrieb, der hier besonders bei der Vermahlung der vielfältigen Produkte eine enorme Erleichterung bei der Produktumstellung bietet. Wegen der besonderen Eigenschaften der Produkte wurden anstatt Plansichter zehn Vibroschleudern eingesetzt. Der ungespritzte Biohafer mit den bekannten wechselnden Qualitäten kommt vor allem von regionalen Demeter-Landwirten. Einige beliefern Bauck schon in der dritten Generation. Reichen die regionalen Ernten nicht, kauft Bauck vom Baltikum oder aus skandinavischen Ländern zu.
Spiegeln und wachsen
Steigt der Produktionsbedarf, ist in der Mühle genug Platz für eine weitere Fertigungsstraße. Das heißt, der Output kann verdoppelt werden. Reicht das immer noch nicht, kann man die neue Hafermühle spiegeln und davor eine weitere Mühle mit den gleichen Abmessungen bauen. Die Fensterfront an der Stirnseite der Mühle dient dann als Übergang und Verbindung beider Mühlen. Hier im Norden gibt es viele Visionen, deshalb haben Geschäftsführung und Betriebsleitung noch einiges vor.

„Es war eine gute Zusammenarbeit“, so das Fazit aller Beteiligten. Natürlich gab es bis zur Inbetriebnahme im Herbst 2020 viel Stress und jede Menge Arbeit. Mit einem 8-Stunden-Tag hätten sie das nicht geschafft. Dennoch ist es in 17 Monaten Bauzeit gelungen, das Gebäude inklusive aller Technik zu erstellen und in Betrieb zu nehmen. Trotz Corona, Lieferengpässen oder schlechtem Wetter. Die Beteiligten waren Profis, es gab schnelle Entscheidungswege und vor allem auch Spaß. Alexander Bachur kann das bestätigen. Er ist jetzt bei Bauck als Betriebsleiter angestellt. Jan-Peter hat auch ihn gebeten zu bleiben.

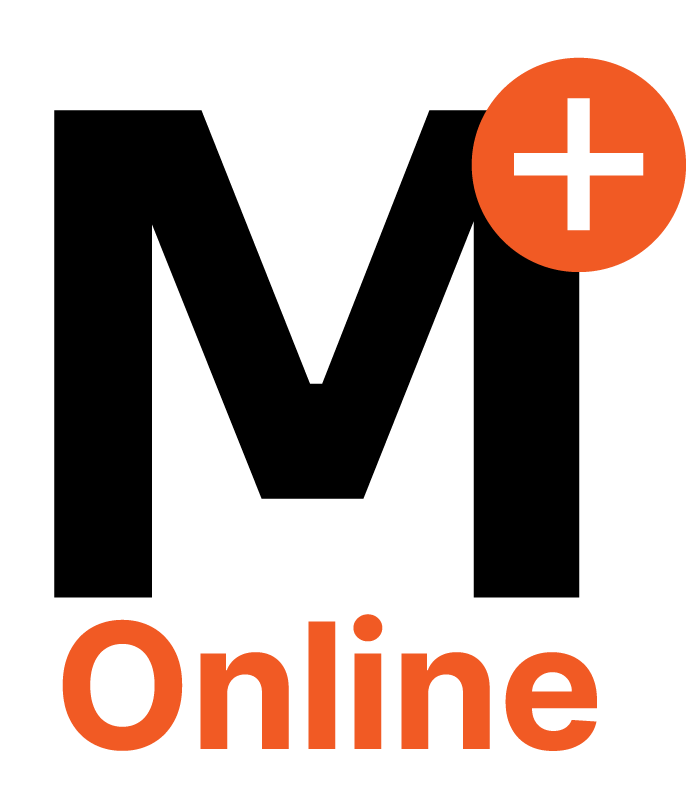
Bereits Abonnent der M+M Print oder Print plus Online ?
Als Abonnent der Mühle + Mischfutter erhalten Sie diesen Zugriff gratis.
Mühle + Mischfutter Online Abo inklusive M+ Online
Unbegrenzter Zugang zu allen M+ Inhalten
Regelmäßiger Newsletter
Bequemer digitaler Zugang
Unterstützung unabhängiger Fachberichterstattung
Meldungen zu diesem Artikel
Weiterlesen
Unsere Experten zu diesem Thema
Personen aus diesem Artikel
Firmen aus dem Artikel
Die Bauck GmbH ist 1969 als einer der Pioniere unter den Naturkostherstellern aus den drei biologisch-dynamisch wirtschaftenden Bauckhöfen in Klein Süstedt, Stütensen und Amelinghausen hervorgegangen. Ursprünglich als Vermarktungsgesellschaft von Demeter-Erzeugnissen gegründet, stellt das Unternehmen heute unter der Marke „Bauck Mühle“ Demeter- und Bio-Produkte wie Mehle, Müslis und Backmischungen in seinen eigenen Mühlen her.